ENVIRONMENTAL PERFORMANCE INROADS FOR SUSTAINABLE DEVELOPMENT DOW | 2021 ESG REPORT | 30 REVOLOOP™ Recycled Plastics Resins: Last year, using our Pack Studios in-house conversion capabilities, we commercialized a global line of mechanically recycled plastic resins, branded REVOLOOP™ resins – a family of products that can be used in either flexible or rigid plastic packaging applications. It’s the first PCR product in Dow’s plastics circularity portfolio to incorporate up to 70% of recycled plastic. In 2021, we sold and launched 12 product grades of REVOLOOP™ resins, with applications ranging from rigid bottles and collation shrink to e-commerce bags and protective packaging. Mattress recycling now a reality with start-up of RENUVA™ plant: By turning end-of-life mattresses into RENUVA™ polyols for use in new mattresses and other applications, our RENUVA™ Mattress Recycling Program is contributing to both a circular and low-carbon economy. In 2021, we launched the world’s first industrial-scale reactor for the chemical recycling of end-of-life mattresses in France. The collective effort brings together Dow Polyurethanes and chemical innovator Orrion Chemicals Orgaform with mattress collector Eco-mobilier, turnkey solutions provider H&S Anlagentechnik and foam manufacturer The Vita Group. When operating at full capacity, the plant will recycle polyurethane foam from up to 200,000 used mattresses per year – mattresses that otherwise would be incinerated. At the new RENUVA™ plant, polyurethane foam from end-of-life mattresses is chemically recycled to create a new polyol, which is a key starting material to produce polyurethane. The RENUVA™ polyol produced from the recycled foam contains approximately 40-45% recycled content and can be tailored for different applications. The first batch of RENUVA™ polyols was delivered to The Vita Group, providing a more sustainable offering to the bedding market. An externally certified lifecycle analysis was conducted for RENUVA™ and found that the process provides a reduction of more than 50% in CO 2 equivalent emissions in comparison with the standard polyol production process. Through collaboration, materials science and innovation, the RENUVA™ Mattress Recycling Program generates value from waste mattresses, addresses the issue of mattress disposal, creates new business ecosystems and at the same time reduces the carbon footprint. Turning Automotive Waste into New Car Products By turning automotive waste into new polyurethane foam-based solutions for vehicle interiors, we are helping car manufacturers meet their market and regulatory demands for more circular products. Created using a mass balance approach, SPECFLEX™ C and VORANOL™ C solutions are made from a circular feedstock produced from recycled and locally obtained automotive waste that replaces virgin fossil fuel-based feedstock. This approach serves as an efficient and validated way for automotive OEMs to reduce greenhouse gas emissions and fossil feedstock inputs, meet regulatory standards and achieve their own ambitious sustainability goals. SPECFLEX™ C and VORANOL™ C are initially being offered through two automotive suppliers, Adient and Autoneum. The new foam systems not only offer the same benefits as current automotive polyurethane foams, such as geometrical adaptability and lightweighting, but also significantly lower the cradle-to-gate carbon footprint of car components. CIRCULAR ECONOMY Sustainability Benefits Circular feedstock using recycled stream from mobility sector Waste reduction in mobility sector 10% CO 2 reduction compared to fossil-fuel equivalent Reliable performance for a wide range of flexible foam systems
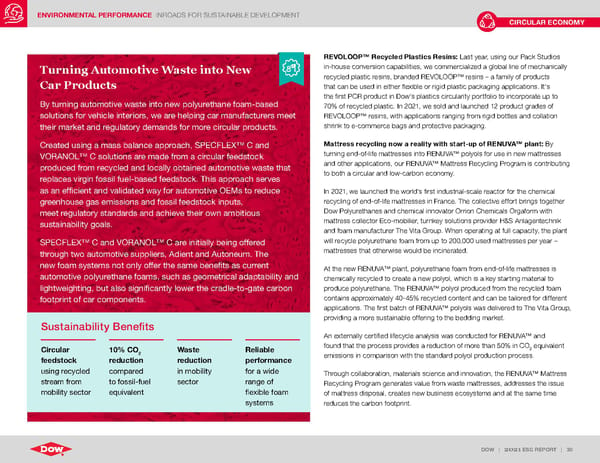