HEALTH & SAFETY INTEGRATING SAFETY INTO ALL WE DO DOW | 2021 ESG REPORT | 40 NEW PERSONAL SAFETY STANDARDS Our continual review of incident trends and near-miss data displayed an opportunity to educate employees and contractors, which led to the creation of the two new standards for safe use. • Dow’s Personal Safety Expertise Center drafted a Hand-Held Portable Tools Standard that included tool design requirements and user guides to help combat incidents associated with equipment such as drills and angle grinders. The standard was tested across six sites and the success of the pilots proved the value of thorough standard development. This standard will be rolled out to all employees and contractors in 15 languages in early 2022. • A new Fatigue Risk Management Standard was piloted across sites in the U.S. Gulf Coast in 2021. An impactful takeaway from these pilots came from feedback sessions, which encouraged transparent conversations for leadership to understand the cultural aspects associated with fatigue. The learnings from the regional rollout helped shape a comprehensive global standard, which will be widely released in 2022. The Contractor Safety Task Force Contractors play a vital role in our operations and, like their Dow counterparts, contractors also engage in potentially high-risk tasks while on the job. The Contractor Safety Task Force was chartered in 2021, with an initial focus on North America and a goal to understand best practices and reinforce positive behaviors that were driving optimal safety performance among contractors. This work led to identifying seven key items for best-in-class contractor safety performance: • Foreperson capability, development and engagement • Observation and intervention programs • Joint Dow/contractor onboarding programs • Strong relationship between Dow and contractor senior leaders • Dow management system reviews of policies, processes, procedures and programs • Forums and opportunities to exchange ideas • Contractor inclusion programs The Task Force’s efforts subsequently led to the development of a Contractor Safety Culture Index and recognition program for top-performing sites, both to be released in 2022. Because of the physical and mental demands of the work environment at our manufacturing sites, fatigue is a real risk. The Fatigue Risk Management Program is about finding a solution to this hidden hazard and driving employee safety to the next level. Kevin Martin, senior operations leader in Freeport, Texas
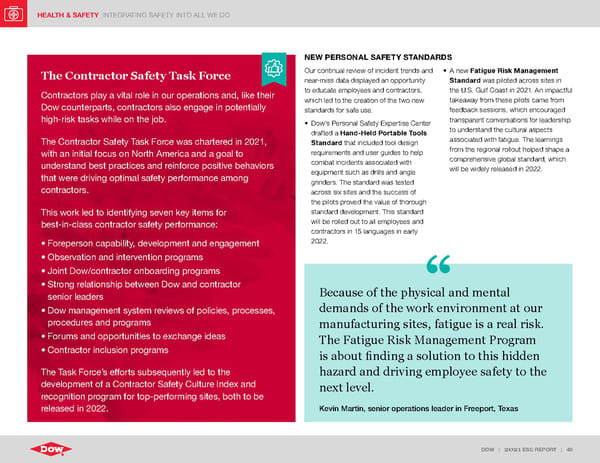